Tangential Flow Filtration in Downstream Bioprocessing
Downstream bioprocessing involves many steps (ex: clarification, chromatography, filtration, etc.) to purify and concentrate a desired molecule produced by natural sources.
One of these methods, tangential flow filtration (TFF), is used in downstream bioprocessing to both:
- Increase the concentration of a molecule in solution based on size (Ultrafiltration)
- Exchange buffers (Diafiltration)
These techniques are used in specific applications such as (but not limited to):
- Removing organic solvents in antibody-drug conjugate manufacturing
- Concentrating plasmid DNA and exchanging chromatographic buffer for the final buffer in plasmid DNA manufacturing
- Increasing concentration for high-viscosity drugs
- Pre-concentrating monoclonal antibodies before anion exchange chromatography
What is Tangential Flow Filtration?
Unlike normal flow filtration (NFF), the feed in TFF flows parallel to the membrane instead of being pushed through the membrane. The advantage here is that in TFF, there is less of a chance for filter clogging, and it is also gentler on shear-sensitive products.
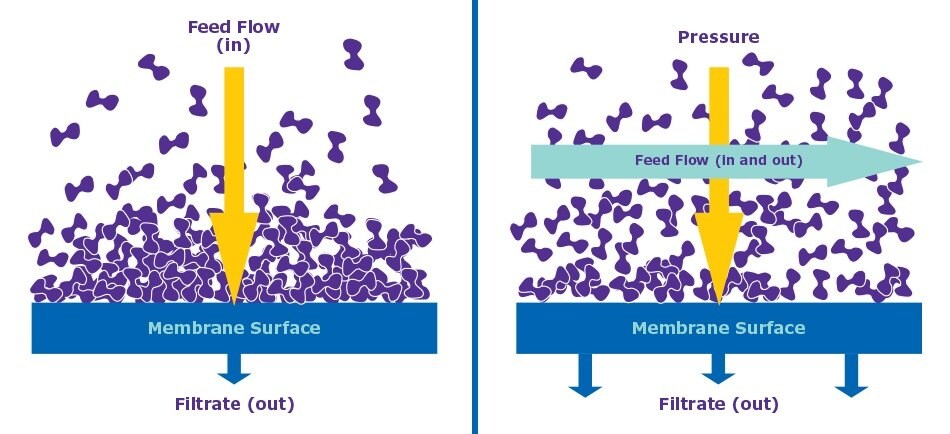
Figure 1.Normal Flow Filtration (NFF) vs. Tangential Flow Filtration (TFF)
There are many ways that TFF can be implemented in the downstream process as described below.
Single-Use Vs. Multi-Use TFF
TFF systems for the filtration of molecules like mAbs, insulin, vaccines, and recombinant proteins have been traditionally operated for reuse. However, reuse of TFF devices requires major steps including cleaning, validation, and storage that add no value to the product, yet require significant time and labor. Single-use TFF (ex: Pellicon® Capsules) eliminates many of the steps of traditional TFF processes to reduce process complexity, save time, and conserve resources in the filtration of mAbs and other biologics.
- Time Savings: Single-use TFF eliminates cleaning steps before and after product processing for increased facility throughput. This could considerably shorten the total process time compared to that of a TFF process with a multi-use device from 7 hours to less than 2.5 hours (Figure 1).
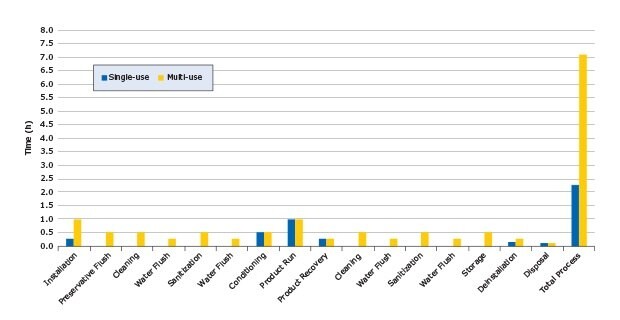
Figure 2.Significant time reduction in a TFF process with single-use TFF as demonstrated using Pellicon® Capsules. Times may vary based on the specific application and process.
- Fluid Savings: Elimination of pre and post-run steps in single-use TFF leads to significant savings of purified water and caustic agents (Table 1), which would minimize the time and labor dedicated to preparing solutions and lower the total cost of fluids during a given filtration process. For example, the total volume of fluid used for multi-use TFF cassettes nears 130 L/m2 while the fluid usage for single-use TFF capsules (ex: Pellicon® Capsules) is about 20 L/m2.
Single-Pass TFF (SPTFF) vs. Traditional Batch TFF
SPTFF differs from traditional batch tangential flow filtration (TFF) in several ways (Figure 2).
Traditional batch TFF requires recirculation of the feed material through the membrane module multiple times to achieve a higher concentration with each passage as the filtrate is removed.
SPTFF uses just one pass through multiple membrane modules connected in series—increasing the path length—to achieve the same volume reduction over time as the traditional batch mode. Due to the single-pass operation, there is no need to return the feed to the original tank, which in many cases can eliminate tankage altogether. Further, SPTFF is typically run at lower feed flow rates to increase conversion of feed to permeate. This allows for smaller pumps and pipe sizes, which reduce hold-up volume within the system and increases product recovery compared to batch TFF. SPTFF is also a gentler option for shear sensitive molecules as the fluid is not passed repeatedly across a membrane. To learn more about implementing and scaling SPTFF, read our technical article.
To discover best practices for assessing different approaches to maximize the benefits of SPTFF concentration and improved productivity of an intensified protein A capture step, watch our webinar.
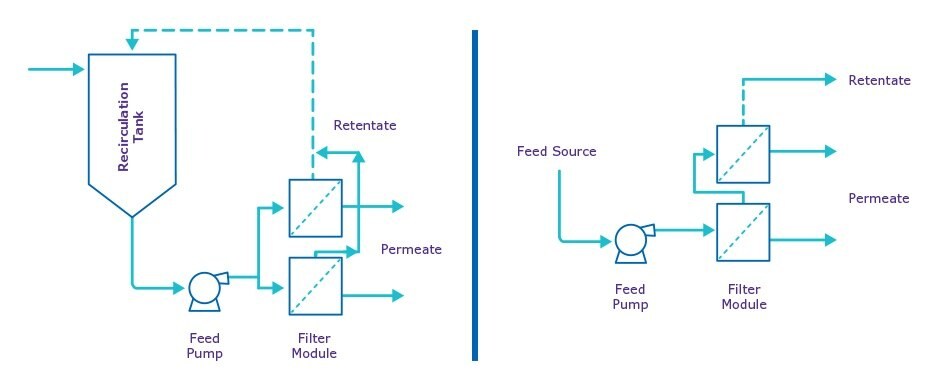
Figure 3.Traditional batch TFF recirculates feed material through the membrane multiple times while single-pass TFF uses multiple membrane modules in series for volume reduction.
These characteristics make SPTFF amenable to intensify chromatography steps by concentrating the solution before loading the column and allowing a smaller amount of resin and buffer to be used. SPTFF also allows for higher concentrated formulations compared to traditional TFF.
To continue reading please sign in or create an account.
Don't Have An Account?