Operational and Financial Advantages of Cellicon® Cell Retention Solution in an N-1 Perfusion Process
Cell Retention Devices in Intensified Upstream Perfusion Processes
Perfusion technology can reduce process time and increase manufacturing capacity of seed train bioreactors without increasing volume requirements. This approach is a key enabler of upstream process intensification as it can achieve higher cell density, run for a longer duration, reduce turnover time, and improve overall product yield and quality.
When a process is run in perfusion mode, a cell retention device (CRD) is used to maintain cells inside the bioreactor while spent media is removed. The Cellicon® Cell Retention Solution along with the Bio4C ACE™ software is scalable to 2,000 L, the standard size of a large-scale single-use bioreactor; this contrasts with other commercially available retention devices that are limited to lower bioreactor working volumes. The ability to scale to 2,000 L offers several operational and financial advantages including the ability to eliminate bioreactors in the seed train.
The following study compared an N-1 perfusion process at the 2,000 L scale using our Cellicon® Cell Retention Solution versus a commercially available cell retention device.
A process scenario was developed using a 2,000 L N-1 perfusion process, which is typically used to seed a fed-batch process at the 10,000 L scale and beyond. The Cellicon® Cell Retention solution was compared to a commercially available cell retention device, which was only scalable to 1,000 L. Thus, the comparison was performed between one 2,000 L bioreactor equipped with one 2,000 L Mobius® Cell Retention System or two 1,000 L systems from another supplier operating in a side-by-side mode. To establish running costs and labor, 5 runs/year were assumed with similar process performance (i.e., no impact in process productivity).
The study evaluated the following parameters:
- Capital investment
- Running costs (mainly consisting of chemicals and consumables)
- Labor hours and costs
- System footprint
Impact of Cellicon® Cell Retention Solution on Capital Expenditures
Capital expenditures were quantified for the cell retention system and associated installation and qualification expenses, assuming that the bioreactors were already in place in the facility. Capital expenditures for the upstream workflow based on the single 2,000 L bioreactor equipped with one Mobius® Cell Retention System 2,000 L were 35% lower than the workflow with two 1,000 L cell retention systems from a different supplier (Figure 1).
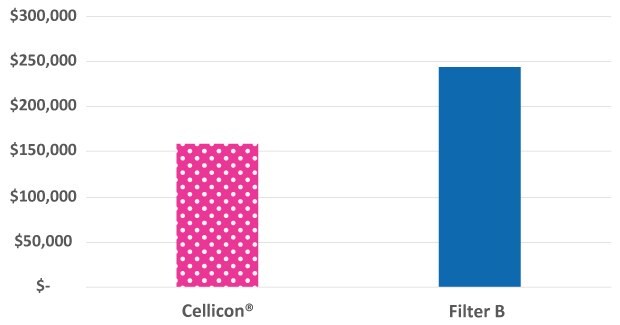
Figure 1.Capital expenditure comparison of the Mobius® Cell Retention System and cell retention system from another supplier operated at a 2,000 L scale.
Impact of Cellicon® Cell Retention Solution on Running Costs
Figure 2 shows a comparison of the costs of chemicals and consumables required to set up and operate the Cellicon® Filter Assembly and the cell retention device from a different supplier. Bags and buffers are required for the prewashing step that must be completed prior to connecting the 1,000 L devices from another supplier to the bioreactor, in contrast to the Cellicon® Filter Assembly which does not require prewashing. The annual consumables costs to run a single Cellicon® device at the 2,000 L scale were 55% less than two devices from a different supplier (assuming 5 runs/year).
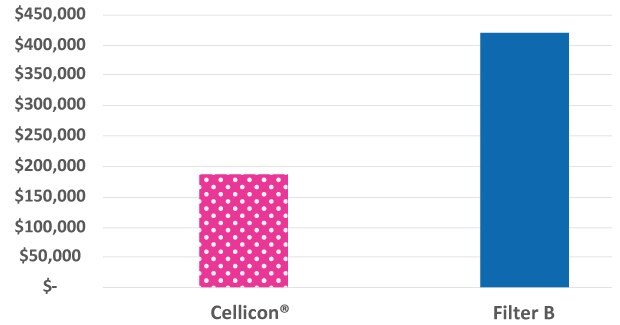
Figure 2.Chemicals and consumables cost comparison of the Cellicon® Cell Retention Solution and another standard cell retention device operated at a 2,000 L scale.
Impact of Cellicon® Cell Retention Solution on Labor Hours and Costs
The plug-and-play Cellicon® Filter Assembly is ready to connect to the bioreactor, offering opportunities to reduce operator time and effort. In contrast, the devices from another supplier require additional manipulation including installing additional assemblies, flushing the filter, and testing for integrity prior to connecting to the bioreactor. Overall, the Cellicon® Filter Assembly required one-third of the time to set up compared to the other devices, significantly reducing labor hours and associated costs (Figures 3A and 3B).

Figure 3.Labor hours required to run the Cellicon® Cell Retention Solution compared to a cell retention device from another supplier at the 2,000 L scale.
Impact of Cellicon® Cell Retention Solution on Facility Footprint
While the Mobius® Cell Retention System is slightly larger than the cell retention system from the other supplier, it includes additional instrumentation and capabilities to monitor the process, such as a perfusate pump, flowmeters, and pressure sensors. These extra features provide process insights that improve decision-making and enable filter performance monitoring to comply with GMP requirements. The annual facility running cost per m2 is used for the comparison shown in Figure 4.
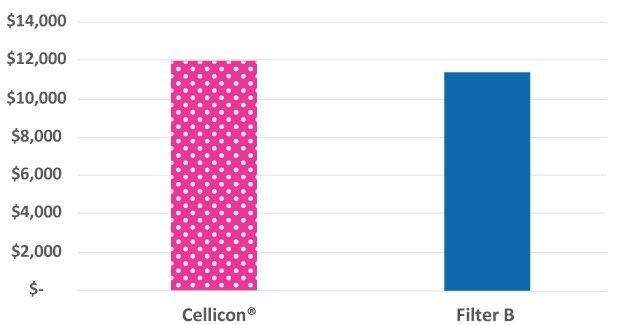
Figure 4.The facility footprint costs for the Mobius® Cell Retention System incorporate additional features while remaining similar in cost to the cell retention device from another supplier.
The Cellicon® Cell Retention Solution offers quantitative and qualitative Benefits
With use of the Cellicon® Cell Retention Solution, capital expenditure savings are more than $85,000 for a 2,000 L process (Figure 5). Assuming five runs per year, the total hard cost savings exceed $230,000 per year or approximately $46,000 per run. Furthermore, it does not require a wetting step and eliminates using additional single-use bags and fluid.
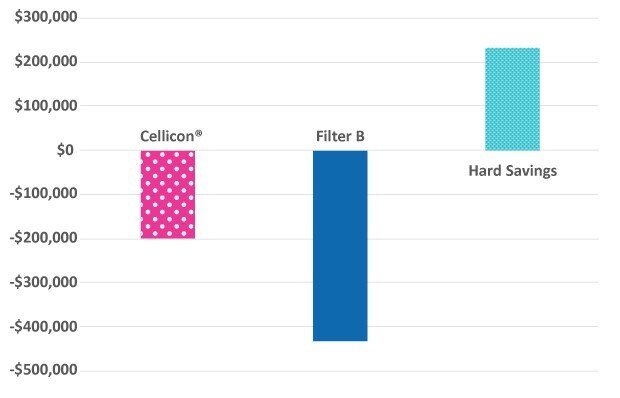
Figure 5.Summary of total hard cost savings with use of the Cellicon® Cell Retention Solution at a 2,000 L scale.
Cellicon® Cell Retention Solution intensifies the Upstream Workflow
The Cellicon® Cell Retention Solution intensifies upstream processes by continuously removing spent media from the bioreactor while retaining high numbers of viable cells. This offers significant financial and operational benefits including:
- Higher cell densities
- Longer duration perfusion runs
- Reliable and reproducible performance
- High throughput and low fouling
- Comprehensive monitoring and precise control
- Predictable linear scale-up from bench-top to manufacturing scale
GraphQL error: Missing locale!
To continue reading please sign in or create an account.
Don't Have An Account?