Removing Viruses From Your Downstream mAb Process
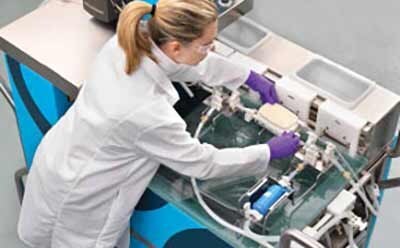
Downstream processing in the production of monoclonal antibodies (mAb) reduces the levels of virus by either removal or inactivation. Regardless of the technology, biomanufacturers must demonstrate the clearance capabilities of different downstream steps as part of the viral safety assessment process.
Downstream processing typically includes:
- Chromatography – virus removal by binding affinity, charge or hydrophobicity
- Chemical treatment – virus reduction by inactivation
- Filtration – virus removal by size exclusion, a critical step for viral safety in most downstream processes
- Demonstrating Effectiveness
Featured Categories
Master biomolecule separation with Ion Exchange (IEX) chromatography. Our anion & cation resins excel in purifying therapeutic molecules, mAbs, proteins, & more.
Enhance biopharma safety and compliance with our virus inactivation solutions, including pasteurization and low pH treatment.
Efficient Filter Integrity Testing: Elevate quality control with Integritest® 5, offering bubble point, diffusion, and hydrophobic testing in-line or offline.
Virus filtration in cell culture media and downstream processes enhances drug safety by minimizing contamination and assuring viral clearance.
Chromatography
To reach viral clearance targets, most downstream processes include at least two chromatography operations. A typical solution is protein A capture, followed by ion exchange chromatography (IEX), comprised of cation exchange chromatography (CEX) to reduce antibody aggregate levels and anion exchange chromatography (AEX) to remove residual host cell proteins and DNA. Under select conditions, both CEX and AEX can contribute to viral safety.
Chemical Treatment
Chemicals used for virus inactivation must meet the same high-quality standards as other raw materials. Selected chemicals should be manufactured or purified to GMP standards (based on the IPEC – PQG GMP guide for pharmaceutical excipients, 2006) for consistent high purity in order to assure process reliability. Chemicals with comprehensive testing and documentation packages simplify the compliance process.
Filtration
Removal of virus by filtration is typically based on size, with most mAb production processes relying on filtration to provide high levels of both enveloped and non-enveloped virus reduction. Virus filtration is regarded as a robust step for virus removal and is relatively insensitive to process conditions. However, the presence of protein aggregates and other trace fouling species can negatively impact the throughput performance of virus filters, resulting in increased filtration area requirements. For greater filtration efficiency, a prefiltration step to remove fouling species may be incorporated, leading to significant improvements in virus filter capacity, flux, and overall viral filtration costs.
Demonstrating Effectiveness
Manufacturers of biologics are required to evaluate their downstream manufacturing process for the ability of selected unit operations to inactivate or remove potential contaminants. Results of such clearance studies are required by regulatory authorities for investigational new drug (IND) submissions. Understanding these regulatory expectations is a key component of clearance study design, informing the manufacturer’s overall viral safety strategy.
Visit our document search for data sheets, certificates and technical documentation.
Related Articles
- Viral safety in bioprocessing relies on a framework of (1) preventing contamination, (2) detecting contamination, and (3) removing or inactivating viral contaminants.
- Preventing adventitious viruses in bioreactors is crucial; manufacturers implement upstream measures to safeguard biotherapeutic manufacturing.
- Molecular testing enhances biomanufacturers' viral safety compliance and speed to results for raw materials and intermediates.
- Monoclonal antibody manufacturing requires scalable solutions ensuring high therapeutic concentration and process safety for immunotherapy.
- Multivariate data analysis (MVDA) makes possible a proactive, real-time approach to monitoring, controlling, and predicting quality and productivity in biomanufacturing. The use of proven software with guided PCA and PLS model creation means you don’t need to be a data scientist to explore and analyze your data.
- See All (13)
Find More Articles and Protocols
How Can We Help
In case of any questions, please submit a customer support request
or talk to our customer service team:
Email custserv@sial.com
or call +1 (800) 244-1173
Additional Support
- Chromatogram Search
Use the Chromatogram Search to identify unknown compounds in your sample.
- Calculators & Apps
Web Toolbox - science research tools and resources for analytical chemistry, life science, chemical synthesis and materials science.
- Customer Support Request
Customer support including help with orders, products, accounts, and website technical issues.
- FAQ
Explore our Frequently Asked Questions for answers to commonly asked questions about our products and services.
Workflow


Detecting viral contamination
Testing for the presence of viruses and other adventitious agents in cell banks, raw materials, and process intermediates.

Monoclonal Antibody Manufacturing
Monoclonal antibody manufacturing is a highly templated approach used to produce mAb-based immunotherapies. Robust, scalable process solutions are required at every step to ensure high therapeutic concentration and process safety, while meeting speed-to-market and cost containment concerns.
Related Webinars
Our head of project management discusses preparing for a viral clearance study from the client perspective with a technical specialist.
Learn how prefiltration technologies can significantly increase the performance of your viral clearance filter.
This presentation describes a case study using Viresolve® Pro membrane filters where virus retention performance is characterized following process interruptions.
In this webinar, you will learn how to simplify validation study design, identify critical processes and feed parameters affecting virus retention, and compile a robust regulatory filing package.
To continue reading please sign in or create an account.
Don't Have An Account?