SMASH Packaging
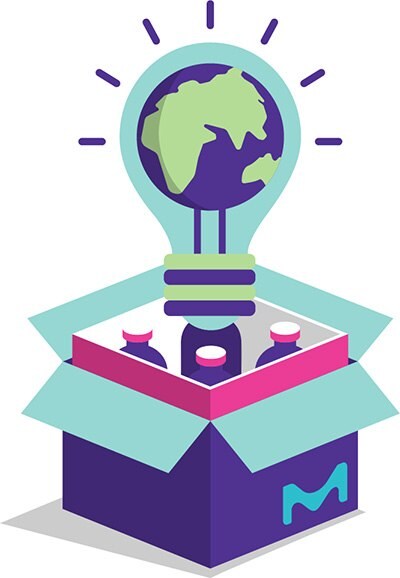
In 2019, we created SMASH Packaging to address the challenging issue of driving improvement in the sustainability of packaging for our 300,000+ diverse products while meeting safety, quality, and performance requirements. The first iteration of SMASH set shorter-term goals from 2019 to 2022 . With SMASH Packaging 2.0, we strive to maximize our impact by driving more systematic and data-driven packaging sustainability improvements.
View our SMASH Packaging Brochure for our comprehensive strategy to tackle packaging sustainability.
Vision and Goals
Our vision is to implement packaging that is designed to minimize our environmental footprint while maintaining or improving the quality and safety of our products. We will do this through our three main SMASH Packaging goals:
- Reduce 10% of packaging weight per unit sales by 2030.
- 100% of fiber packaging to be deforestation-free by 2030.
- 100% of packaging to be designed following circular design principles by 2030.
These three goals will contribute to reducing our packaging greenhouse gas emissions to support our sustainability strategy.
Our Approach
With over 100 packaging improvement projects driven by colleagues across the organization, SMASH has established the foundational principles of packaging sustainability and has contributed to important changes such as the annual reduction of 400+ metric tons of packaging or the development of greener coolers for our cold chain shipments. Each packaging improvement project is just one step to reach our long-term sustainability goals.
From consultation with internal and external packaging and sustainability experts, we identified four pillars that are the foundations of our SMASH Packaging strategy. Based on these four pillars also known as the four S's —SHRINK, SECURE, SWITCH, and SAVE, we set specific 2030 goals to drive more packaging sustainability across our organization and realize our packaging sustainability vision.
Packaging Vision: Packaging that is designed to minimize our environmental footprint without compromising the quality or safety of our products.
2030 Goals |
Reduce 10-15% of packaging weight per unit sales by 2023 | 100% of fiber packaging to be deforestation free by 2030 | 100% of packaging to be designed following circular design principles by 2030 | |
Pillars |
![]() |
![]() |
![]() |
![]() |
Shrink |
Secure |
Switch |
Save |
|
Reduce Amount of Packaging |
Achieve Zero Deforestation |
Improve Material Sustainability |
Maximize Circularity |
|
Our aim is to eliminate the use of packaging that is excessive in size or weight which is unnecessarily consumes more resources, increases energy use and air emissions during transportation. | Our aim is to ensure that the wood and fiber-based packaging materials that we use do not contribute to deforestation. | Our aim is to improve the sustainability of plastic materials by increasing the use of materials with lower environmental impacts and reducing the use of plastics produced with chemicals of concern. | Our aim is to eliminate the use of packaging materials that are not compatible with recycling and providing customers with recycling guidance for our packaging materials. |
Our Progress
We use the SMASH Packaging framework to inform, implement, and measure our sustainable packaging projects across all of our sites around the world.
Topline Results
- 400+ metric tons of packaging is avoided annually through SMASH Packaging projects.
- 72.9% of all fiber packaging comes from deforestation free certified materials, a 10% increase from 2019.
- 65% of new product development packaging projects aligned with SMASH Packaging standards.
Shrink — Reduce the Amount of Packaging
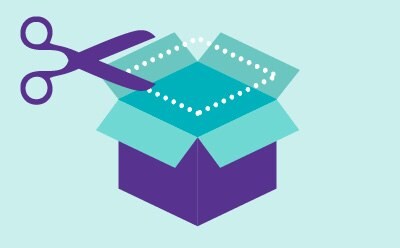
Our aim is to eliminate the use of packaging that is excessive in size or weight which unnecessarily consumes more resources, increases energy use and air emissions during transportation. Excess packaging is also undesirable for our customers since there are costs associated with the management and disposal of the packaging. Currently 400+ metric tons of packaging is avoided annually through SMASH Packaging projects.
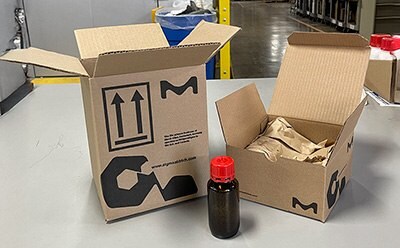
Packaging for Smalls
We are tackling unused airspace by reducing the size of packaging in our small products. A smaller box was developed and validated for shipping around 1,000 products daily at our Milwaukee distribution center. The new solution has an air space reduction of over 50%– a reduction of 60 metric tons of packaging materials annually. We are further developing this initiative by shipping more products in these boxes and implementing other Packaging for Smalls projects at sites across the organization.
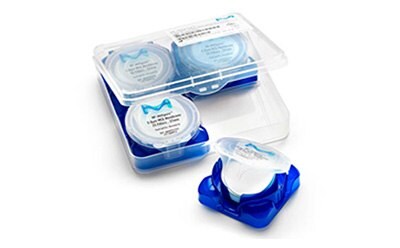
Cut Disc Membrane Packaging
The packaging system for our cut disc membrane, produced in Cork, Ireland, was redesigned to reduce plastic and improve usability. The previous packaging system was made of polystyrene which was brittle and difficult to open. The new packaging system is made of polypropylene (PP) which has a lower carbon footprint than polystyrene (PS). This improved usability and reduced plastic per unit by 22%, representing 8 tons of plastic annually.

Bulk Packaging for Millistak+® Pods
Millistak+® HC, HC Pro, and Clarisolve Pods now have the option to be shipped through a bulk packaging solution. The new Bulk Packs consist of an innovative packaging system developed to optimize the number of units per pallet and reduce the amount of packaging compared to a single pack. Buying in bulk now offers between 33% to 53% less packaging waste depending on the product. It also leads to a significant reduction in operator time to open and manage the product and packaging.
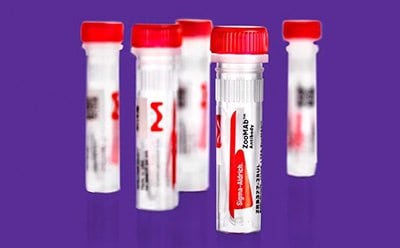
ZooMAb® Packaging
ZooMAb® antibodies were developed as a lyophilized product, which makes the antibodies shippable at ambient temperature. This means that we can ship them in a standard shipping box, resulting in dramatic reduction of the weight of packaging for the shipment of the products, and increase of packaging recyclability. This improvement avoids the use of 4 metric tons of distribution packaging annually including insulating shipping container and ice bricks, saving about 18 metric tons of CO2e.
Secure — Achieve Zero Deforestation
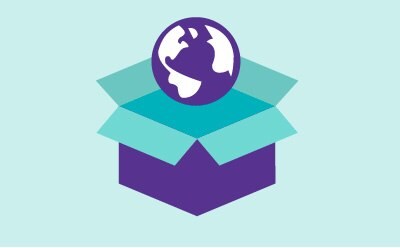
Deforestation is a source of global warming and is a threat to biodiversity. Our aim is to ensure that the wood and fiber-based packaging materials that we use do not contribute to deforestation. So far, 72.9% of all fiber packaging aligns with our zero deforestation standards a 10% increase from 2019.

Folded Boxes in Darmstadt
In Darmstadt, we switched to materials with sustainable forestry certification for key vendors for folded boxes which represents approximately 76 tons of material annually.

Corrugated Boxes in Molsheim
We worked with our key corrugated vendors at our Molsheim site to progressively add sustainable forestry certification for most of our corrugated packaging materials. This represents approximately 1,000 tons of materials and more than 90% of the total amount of corrugated packaging used by the site annually.
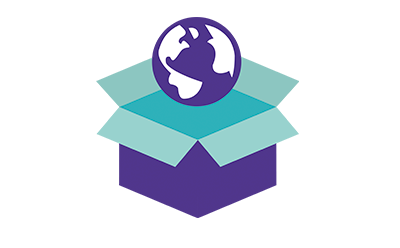
Corrugated Boxes in Songdo
In 2022, the distribution center in South Korea transitioned to using materials with sustainable forestry certification for their corrugated boxes. This change impacted approximately 100 tons of material usage annually.
Switch — Improve Material Sustainability
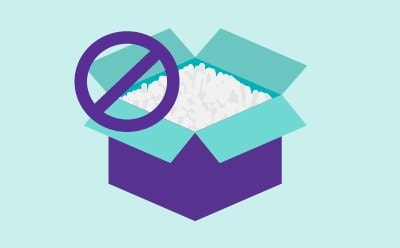
Our aim is to improve the sustainability of packaging materials by increasing the use of materials with lower environmental impacts and reducing the use of materials produced with chemicals of concern.
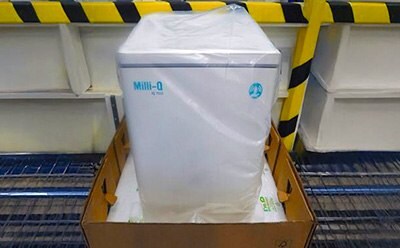
Milli-Q® Protective Foam
Recent Milli-Q® systems were protected by conventional petroleum-based polyethylene foam. The new foam protectors are now made from bio-based polyethylene that stems from a coproduct of sugar production and reduced the usage of fossil-based sources.
This reduces the usage of fossil-based polyethylene foam by 4 tons annually and reduces CO2 emissions by 8.8 tons of CO2e annually.
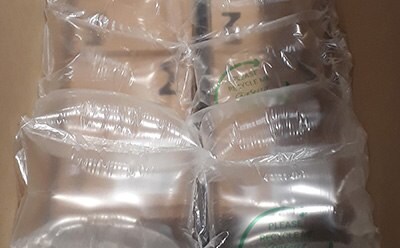
Plastic Air Pillows
Our Strasbourg distribution center team changed air pillows used for cushioning to use less materials and more recycled content. In 2022, the change of air pillows from virgin ones to the version with lower thickness and 50% recycled content led to an annual reduction of 9 metric tons plastic and 26 metric tons CO2e.
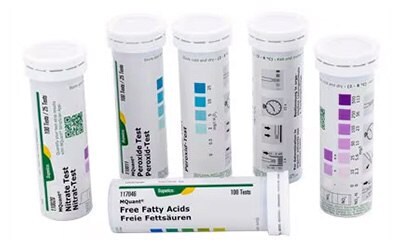
Test Strips Aluminum Tubes
We introduced recycled content for the aluminum tube used to pack our test strips. The primary packaging tube material used to hold the test strips was switched from virgin aluminum to aluminum that consists of 60% post-industrial recycled aluminum and 40% internal aluminum scrap. These changes are being implemented progressively across our test strips product portfolio, overall affecting 40 million strips per year. This will ultimately lead to savings of 56 tons of CO2e annually.
Save — Maximize Circularity
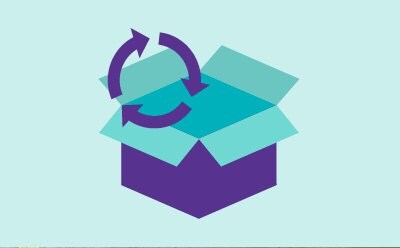
Our aim is to maximize circularity of our packaging materials by developing reusable packaging and associated reuse programs, eliminating the use of packaging materials that are not compatible with recycling, and by providing our customers with recycling guidance for all our packaging materials.
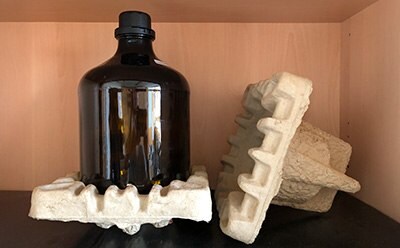
Molded Pulp Inserts
We have been replacing EPS with molded components made of cellulose and recycled paper pulp to pack a variety of liter glass bottle configurations in shipping boxes, thereby replacing about three million EPS parts per year. We recently completed a replacement project at our Darmstadt distribution center for individual shipments of 1x1L, 1x1.6L, 1x2.5L, and 4x1L. The new, recyclable pulp-based components annually replace 251,000+ parts.
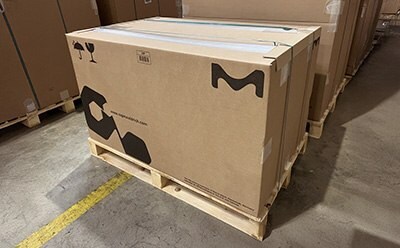
Pallet Edge Protectors
Pallet edge protectors for shipping boxes in Darmstadt previously contained a mix of paper and plastic. We replaced them with 100% paper-based and deforestation-free-certified edge protectors with identical performance, avoiding the use of 3.5 tons of plastic and 4.8 tons of CO2e annually.
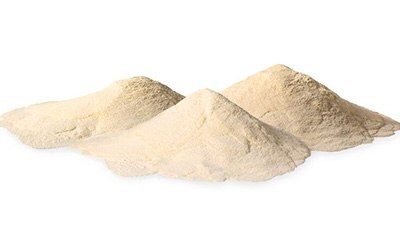
EcoCult® Packaging
In Darmstadt, we redesigned the packaging of our EcoCult® dehydrated cultured media in alignment with our SMASH Packaging standards. Typically shipped in a plastic drum, we replaced it with a plastic bag and a corrugated box allowing to significantly reduce the environmental impacts related to the packaging of the product while ensuring the same protection. These changes led to a 62% packaging weight reduction and a 95% non-renewable packaging materials reduction.
Curious to learn more about our SMASH Packaging Plan? Check out our SMASH Packaging brochure for more details about how we implement our SMASH Packaging framework across the organization.
Our Commitment
SMASH Packaging is committed to increasing the sustainability of our packaging while meeting safety, quality and performance requirements. Not only are we revisiting past products, but we also carefully consider greener packaging solutions for all new products thanks to the Design for Sustainability framework.
Redesigning packaging is a complex process— from the box size to the tape, the padding materials to the labels. Safety is our top priority when we redesign packaging. Shipping breakable, sensitive and hazardous goods, is tightly regulated, and packaging engineers must run any packaging change through tests to ensure the change is safe. Given these challenges, we introduce any change on a small scale first, and over time, roll out the changes to other sites. Additionally, we continually work to validate each project to transparently share the environmental impact of each project. We conduct life-cycle assessments and work with 3rd party consultants to measure the weight and carbon footprint reductions for each packaging update.
To continue reading please sign in or create an account.
Don't Have An Account?